Fehlermöglichkeits- und Einflussanalyse: Ein Überblick
"Alles, was schief gehen kann, wird auch schief gehen" - Murphys allgemeines Gesetz
Was ist FMEA?
Die Fehlermöglichkeits- und -einflussanalyse (FMEA) ist ein systematischer Ansatz, um wahrscheinliche Fehler in einem System, Produkt oder Prozess zu identifizieren, ihre Auswirkungen zu bewerten und herauszufinden, wie sie minimiert oder verhindert werden können. Die FMEA ist eine proaktive Methode, die darauf abzielt, künftige Probleme vorherzusehen und sich mit ihnen zu befassen, bevor sie auftreten, anstatt erst im Nachhinein auf sie zu reagieren. Zuverlässigkeit, Sicherheit und Qualitätskontrolle werden in der technischen Entwicklung häufig durch den FMEA-Prozess berücksichtigt.
Um wahrscheinliche Fehlermodi, ihre Folgen und ihre Ursachen zu ermitteln, überprüft ein Expertenteam, das einen grundlegenden FMEA-Prozess durchführt, ein System, ein Produkt oder einen Prozess gründlich. Auf der Grundlage des Schweregrads, der Wahrscheinlichkeit des Auftretens und der Erkennbarkeit weist das Team dann jedem wahrscheinlichen Fehlermodus eine Bewertung zu. Die möglichen Fehlerarten werden anhand der bereitgestellten Informationen nach ihrer Wichtigkeit eingestuft. Das Team erarbeitet dann Maßnahmen zur Vermeidung oder Minimierung der kritischsten Fehlerszenarien und setzt diese um.
Die FMEA fördert einen proaktiven Ansatz zur Problemlösung, was einer ihrer Hauptvorteile ist. Unternehmen können Schwierigkeiten vermeiden oder verringern, indem sie sie im Voraus erkennen und Maßnahmen ergreifen, wodurch sie Zeit und Geld sparen. Die Untersuchung von "Was-wäre-wenn"-Szenarien wird durch den qualitativen Prozess der FMEA gefördert, der dazu genutzt werden kann, wahrscheinliche Fehlerarten zu finden, die mit anderen Methoden nicht erkennbar wären.
Das ultimative Ziel der FMEA ist es, die Wahrscheinlichkeit von kritischen Fehlern zu begrenzen oder ganz auszuschalten. Organisationen können die Zuverlässigkeit, Sicherheit und Qualität ihrer Waren und Dienstleistungen verbessern, was die Zufriedenheit und Loyalität ihrer Kunden erhöht, indem sie einen systematischen Ansatz zur Identifizierung und Lösung möglicher Probleme verfolgen.
Geschichte Fakten
Um wahrscheinliche Ausfälle und deren Auswirkungen auf die militärische Ausrüstung zu bewerten, entwickelte das US-Militär in den 1940er Jahren die FMEA. Das Militär nutzte die FMEA, um das Risiko von Ausfällen während des Betriebs zu verringern und die Zuverlässigkeit der Ausrüstung zu gewährleisten.
Die Luft- und Raumfahrtindustrie nutzte die FMEA erstmals in den 1960er Jahren, um mögliche Risiken und Produktausfälle zu bewerten, und sie wurde schnell zu einem entscheidenden Schritt in ihren Konstruktions- und Produktionsprozessen. In den 1970er Jahren wurde die FMEA von der Automobilindustrie eingeführt, um die Sicherheit und Zuverlässigkeit ihrer Fahrzeuge angesichts der zunehmenden Komplexität der Fahrzeugsysteme zu gewährleisten.
In den 1980er Jahren wurde die FMEA von mehreren Branchen als zuverlässige Technik zur Erkennung wahrscheinlicher Fehler übernommen. In dieser Zeit entwickelte die Society of Automotive Engineers (SAE) einen Standardansatz für die FMEA-Implementierung, der bewährte Verfahren für die Anwendung der FMEA in verschiedenen Branchen umfasste.
Ein neuer Standard, die Design-FMEA (DFMEA), die ausschließlich für die Untersuchung von Risiken und potenziellen Fehlern im Zusammenhang mit dem Produktdesign verwendet wird, wurde 2008 veröffentlicht. Als Weiterentwicklung der konventionellen FMEA-Methode konzentriert sich die DFMEA auf die Lokalisierung und Vermeidung von Fehlern in der Konstruktionsphase selbst.
Das AIAG-VDA FMEA-Harmonisierungsprojekt, das mehrere FMEA-Standards und -Leitfäden sektorübergreifend vereinheitlichen soll, hat der FMEA 2019 ein neues Gesicht gegeben. Durch die Beseitigung von Redundanzen und die Straffung der Technik versuchte diese Initiative, die Effizienz und Effektivität des FMEA-Prozesses zu verbessern.
Wie führt man eine FMEA durch?
FMEA-Prozess nach AIAG-VDA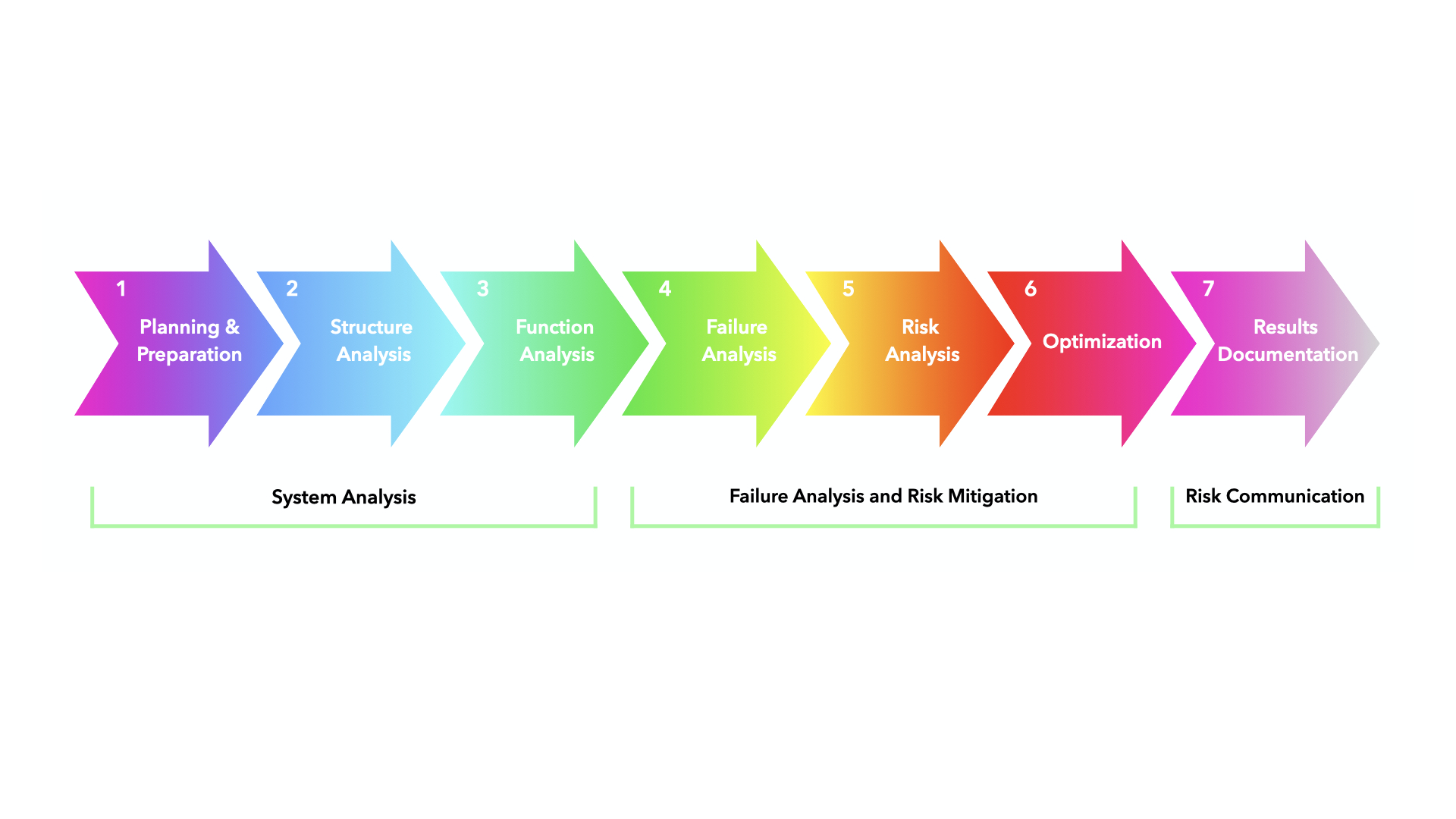
Figure 1 - AIAG-VDA FMEA process
Das FMEA-Verfahren ist in dem weit verbreiteten AIAG-VDA FMEA-Handbuch ausführlich beschrieben. Hier finden Sie eine Liste aller erforderlichen Schritte:
- Planung und Vorbereitung. Aufstellung von Grundregeln und Zeitplänen, Zusammenstellung des Teams und Festlegung der Ziele und des Umfangs der FMEA.
- Strukturanalyse. Erstellen Sie ein Blockdiagramm oder ein Prozessablaufdiagramm, definieren Sie das zu untersuchende System oder den Prozess und listen Sie dessen Funktionen und Bedürfnisse auf.
- Funktionsanalyse. Bestimmen Sie die möglichen Fehlermodi für jede Funktion und deren Auswirkungen auf den Prozess oder das System.
- Fehleranalyse. Bestimmen Sie die Ursachen für jeden Fehlermodus und schätzen Sie das Ausmaß ein, in dem der Prozess oder das System davon betroffen ist.
- Risikoanalyse. Bestimmung der vorhandenen Kontrollen zur Verhinderung oder Erkennung von Fehlern durch Bewertung der Häufigkeit und Wahrscheinlichkeit des Auftretens jedes Fehlermodus.
- Optimieren. Erarbeitung von Empfehlungen zur Verringerung des Schweregrads, des Auftretens und der verstärkten Erkennung von Fehlertypen mit hohem Risiko.
- Dokumentation der Ergebnisse. Dokumentieren Sie die Ergebnisse der FMEA, einschließlich der vorgeschlagenen Maßnahmen und des Status der Ausführung dieser Maßnahmen.
Jeder Schritt ist sequentiell, d.h. der vorherige Schritt erzeugt Ausgabedaten, die als Input für den nächsten Schritt dienen.
Das AIAG-VDA FMEA-Handbuch bietet auch Empfehlungen zur Bewertung von Schweregrad, Auftreten und Erkennungsgrad sowie zur Definition von Gegenmaßnahmen für risikoreiche Fehlerarten. Um eine kontinuierliche Verbesserung des zu analysierenden Systems oder Prozesses zu gewährleisten, sollte der iterative FMEA-Ansatz häufig überprüft werden.
FMEA-Fall: Auftragsabwicklung in einem Online Shop
In diesem Artikel wird der FMEA-Prozess am Beispiel des Auftragsabwicklungsprozesses in einem Online-Shop analysiert.
Definieren Sie Umfang und Ziele
Zunächst müssen der Umfang und der Zweck der FMEA festgelegt werden. Dies beinhaltet die Festlegung des zu analysierenden Produkts oder Prozesses, des Zwecks der Analyse und des Expertenteams, das die Analyse durchführen wird. Es ist wichtig zu beachten, dass das Team wirklich funktionsübergreifend sein sollte, d.h. mit Personen, die unterschiedliche Kenntnisse über den Prozess, das Produkt oder die Dienstleistung und die Kundenbedürfnisse haben. Das heißt, dieser Prozess wird nicht nur von einem Teammitglied (z. B. einem Business Analysten oder Projektmanager) durchgeführt, sondern fast alle internen und externen Interessengruppen sollten daran teilnehmen.
Für die vorliegende Fallstudie wird zunächst beschrieben, was genau untersucht werden soll, nämlich der Prozess der Annahme, Auswahl und Verpackung sowie der Auslieferung von Bestellungen. Der nächste Abschnitt zeigt, warum und zu welchem Zweck dies geschieht. Außerdem wird ein funktionsübergreifendes Team benannt, das diese Analyse durchführen wird.
Scope |
Objectives |
Team members |
The Order Fulfillment process, which comprises the stages of receiving, selecting and packaging, and delivering orders, will be the subject of the FMEA study. |
1. Identify potential failure modes and associated risks in the Order Fulfillment process. 2. Prioritize failure modes based on their severity and occurrence, and develop appropriate corrective actions to reduce the risks. 3. Verify the effectiveness of corrective actions and establish ongoing monitoring and measurement to ensure sustained effectiveness. 4. Improve product quality, reduce customer complaints, and increase process efficiency. |
Operations Manager Production Manager Shipping Manager Quality Manager IT Manager Customer Service Representative |
Identifizieren Sie mögliche Fehler und Auswirkungen
Als Nächstes sollten alle potenziellen Fehlerarten und ihre Auswirkungen ermittelt werden. Dies kann durch ein Brainstorming, die Überprüfung historischer Daten oder andere Instrumente wie z. B. eine Fehlerbaumanalyse erfolgen.
Failure Mode |
Effect |
Incorrect item shipped |
Customer dissatisfaction, potential returns and refunds, potential loss of revenue |
Incorrect quantity shipped |
Customer dissatisfaction, potential returns and refunds, potential loss of revenue |
Delayed shipment |
Customer dissatisfaction, potential loss of revenue, potential damage to customer relationship |
Damaged product during shipping |
Customer dissatisfaction, potential returns and refunds, potential loss of revenue, potential damage to customer relationship |
Bewertung von Schweregrad, Auftreten und Nachweisbarkeit
Sobald die potenziellen Fehler identifiziert sind, müssen Schweregrad, Auftreten und Erkennbarkeit jedes Fehlers bewertet werden.
Der Schweregrad gibt an, wie schwerwiegend die Auswirkungen eines Fehlers auf den Kunden oder Endbenutzer sind. Das Auftreten ist die Wahrscheinlichkeit oder Häufigkeit des Auftretens des Fehlers. Und die Erkennbarkeit ist die Fähigkeit der derzeitigen Kontrollen oder Systeme, den Fehler zu erkennen, bevor er den Kunden oder Endbenutzer erreicht. Die Punktzahlen werden von der im ersten Schritt ermittelten Expertengruppe quantifiziert.
Failure Mode |
Effect |
Severity Rating |
Occurrence Rating |
Detection Rating |
Incorrect item shipped |
Customer dissatisfaction, potential returns and refunds, potential loss of revenue |
8 |
4 |
9 |
Incorrect quantity shipped |
Customer dissatisfaction, potential returns and refunds, potential loss of revenue |
7 |
3 |
8 |
Delayed shipment |
Customer dissatisfaction, potential loss of revenue, potential damage to customer relationship |
6 |
5 |
7 |
Damaged product during shipping |
Customer dissatisfaction, potential returns and refunds, potential loss of revenue, potential damage to customer relationship |
9 |
2 |
8 |
Skalen für die Bewertung
Eine Reihe von Skalen wird typischerweise verwendet, um die Schwere, die Häufigkeit des Auftretens und die Erkennbarkeit von potenziellen Fehlern während einer FMEA zu bewerten. Diese Skalen werden verwendet, um jedem Fehlermodus eine numerische Bewertung zuzuweisen, was die Berechnung einer Risikoprioritätszahl (RPZ) ermöglicht.
Einige der verwendeten Skalen sind:
- Schweregrad. Eine Skala von 1 bis 10, wobei 1 die geringste und 10 die höchste Schwere darstellt. Die Einstufung des Schweregrads basiert auf den potenziellen Auswirkungen des Fehlermodus auf den Kunden oder Endbenutzer.
- Auftreten. Eine Skala von 1 bis 10, wobei 1 für die geringste und 10 für die höchste Wahrscheinlichkeit steht. Die Häufigkeitsbewertung basiert auf der Wahrscheinlichkeit des Auftretens des Fehlermodus.
- Erkennbarkeit. Eine Skala von 1 bis 10, wobei 1 die höchste Erkennbarkeit und 10 die geringste Erkennbarkeit darstellt. Die Bewertung der Erkennbarkeit basiert auf der Leichtigkeit, mit der der Fehlermodus erkannt wird, bevor er ein Problem verursacht.
Einige Organisationen modifizieren diese Skalen, um sie ihren Bedürfnissen anzupassen.
Figure 2 - Scales for Evaluation
Risikoberechnung - Risikoprioritätszahl (RPZ)
Als nächstes muss die Risikoprioritätszahl (RPZ) für jede Fehlerart berechnet werden. Die RPZ wird durch Multiplikation der Werte für Schweregrad, Häufigkeit und Entdeckbarkeit berechnet. Daraus ergibt sich ein numerischer Wert, der dabei hilft, Prioritäten zu setzen, welche Fehler zuerst behandelt werden sollten. Die FMEA-Dokumente enthalten die folgenden Vorlagen für die endgültige Bewertung der Risikopriorität.
Figure 3 - RPN Calculation
Failure Mode |
Effect |
Severity Rating |
Occurrence Rating |
Detection Rating |
RPN |
Incorrect item shipped |
Customer dissatisfaction, potential returns and refunds, potential loss of revenue |
8 |
4 |
9 |
288 |
Incorrect quantity shipped |
Customer dissatisfaction, potential returns and refunds, potential loss of revenue |
7 |
3 |
8 |
168 |
Delayed shipment |
Customer dissatisfaction, potential loss of revenue, potential damage to customer relationship |
6 |
5 |
7 |
210 |
Damaged product during shipping |
Customer dissatisfaction, potential returns and refunds, potential loss of revenue, potential damage to customer relationship |
9 |
2 |
8 |
144 |
Es ist wichtig zu beachten, dass die RPZ keine endgültige Bewertung von Fehlern darstellt. Sie ist lediglich ein Hilfsmittel, um Prioritäten zu setzen, welche Fehler zuerst angegangen werden sollten. Das FMEA-Team sollte sein Urteilsvermögen und seine Erfahrung nutzen, um zu bestimmen, welche Fehler die kritischsten sind.
Identifizierung und Umsetzung von Korrekturmaßnahmen
Sobald die RPZ berechnet ist:
- Identifizierung potenzieller Abhilfemaßnahmen für risikoreiche Fehlermodi auf der Grundlage von RPZ-Werten und anderen relevanten Faktoren.
- Priorisierung der Korrekturmaßnahmen auf der Grundlage von Durchführbarkeit, Kosten und möglichen Auswirkungen auf Kundenzufriedenheit und Umsatz.
- Zuweisung der Verantwortung für die Durchführung von Korrekturmaßnahmen und Festlegung von Zeitplänen für die Fertigstellung.
Es gibt eine inoffizielle Regel, die besagt, dass, wenn ein Fehlermodus eine niedrige Priorität hat, die Korrekturmaßnahmen für diesen Modus nicht oder zuletzt durchgeführt werden.
Failure Modes |
Potential Corrective Actions |
Priority |
Responsible Person |
Timeline |
Incorrect item shipped |
Implement double-check system for order picking and shipping |
High |
Operations Manager |
4 weeks |
Incorrect quantity shipped |
Implement barcode scanning system for order picking and shipping |
High |
IT Manager |
6 weeks |
Delayed shipment |
Improve communication between production and shipping teams to identify potential delays earlier |
Medium |
Production Manager and Shipping Manager |
8 weeks |
Damaged product during shipping |
Improve packaging materials and methods to reduce damage during shipping |
Medium |
Quality Manager |
10 weeks |
Überprüfung der Wirksamkeit von Abhilfemaßnahmen
Schließlich muss die Wirksamkeit der getroffenen Abhilfemaßnahmen überprüft werden. Dieser Schritt beinhaltet:
- Überwachung der Durchführung von Korrekturmaßnahmen und Überprüfung ihrer Wirksamkeit im Hinblick auf die Verringerung des Risikos hochprioritärer Fehlerarten.
- Erstellung eines Plans für die laufende Überwachung und Messung, um die nachhaltige Wirksamkeit der Korrekturmaßnahmen zu gewährleisten.
- Kommunikation der Ergebnisse der Verifizierung von Korrekturmaßnahmen an die relevanten Interessengruppen und Aktualisierung der FMEA-Analyse, falls erforderlich.
Corrective Actions |
Verification Plan |
Results |
Updated RPN |
Implement double-check system for order picking and shipping |
During a month, do daily reviews of the order selection and shipping records. |
No instances of incorrect item shipped during the audit period |
48 |
Implement barcode scanning system for order picking and shipping |
During two months, examine order picking and shipping logs on a weekly basis. |
No instances of incorrect quantity shipped during the audit period |
24 |
Improve communication between production and shipping teams to identify potential delays earlier |
During three months, have weekly meetings between the production and shipping teams. |
Number of delayed shipments decreased by 50% during the verification period |
105 |
Improve packaging materials and methods to reduce damage during shipping |
During six months, do monthly reviews of consumer comments and returns. |
Number of customer complaints and returns related to damaged products decreased by 80% during the verification period |
29 |
Es ist wichtig, daran zu denken, dass die FMEA ein fortlaufender Prozess ist und ständig überprüft und aktualisiert werden sollte, wenn neue Informationen verfügbar werden.
Dokumentation - Das FMEA-Formular
Sie ist eigentlich nicht der letzte Schritt des Prozesses, sondern wird parallel zu anderen Aktivitäten durchgeführt. Die FMEA wird in der Regel in einem Formular dokumentiert, in dem alle während der Analyse gesammelten Informationen festgehalten werden. Das Formular enthält in der Regel Informationen wie das analysierte Produkt oder den Prozess, potenzielle Fehlerarten, Schweregrad, Wahrscheinlichkeit des Auftretens, Nachweisbarkeit, RPZ und ergriffene Korrekturmaßnahmen. Es ist wichtig, noch einmal zu betonen, dass dieses Formular vom gesamten Team während der Analyse, während der Korrekturmaßnahmen und nach den Korrekturmaßnahmen ausgefüllt wird, was bedeutet, dass dieser Prozess fortlaufend ist und nicht einfach erledigt und vergessen wird.
Figure 4 - FMEA form
FMEA-Schlüsselprinzipien
So können nun die wichtigsten Grundsätze, die FMEA-Ideologie, definiert werden, die Folgendes umfassen
- Vorbeugen ist besser als aufdecken. Die FMEA zielt darauf ab, potenzielle Fehler zu erkennen, bevor sie auftreten, so dass proaktive Maßnahmen ergriffen werden können, um sie von vornherein zu verhindern. Dieser Ansatz ist effektiver und effizienter als der Versuch, Probleme zu entdecken und zu beheben, nachdem sie bereits aufgetreten sind.
- Systematischer Ansatz. Die FMEA ist ein systematischer Ansatz, der einen teambasierten Ansatz zur Identifizierung potenzieller Fehlermöglichkeiten, ihrer Ursachen und ihrer Auswirkungen auf das System beinhaltet. Mit diesem Ansatz wird sichergestellt, dass alle potenziellen Fehlermöglichkeiten identifiziert und analysiert werden.
- Risikopriorisierung. Die FMEA verwendet einen risikobasierten Ansatz, um potenzielle Fehler auf der Grundlage ihrer Schwere, ihres Auftretens und ihrer Entdeckbarkeit zu priorisieren. Dies hilft, die Ressourcen auf die kritischsten Fehlerarten zu konzentrieren und ermöglicht ein effektives Risikomanagement.
- Kontinuierliche Verbesserung. Die FMEA ist ein iterativer Prozess, der zur kontinuierlichen Verbesserung von Produkten, Prozessen und Dienstleistungen eingesetzt wird. Die Ergebnisse der FMEA können als Grundlage für Konstruktionsverbesserungen, Prozessänderungen und andere Korrekturmaßnahmen zur Verringerung des Fehlerrisikos dienen.
- Funktionsübergreifende Zusammenarbeit. Die FMEA erfordert die Zusammenarbeit zwischen verschiedenen Funktionen und Abteilungen innerhalb einer Organisation, um sicherzustellen, dass alle potenziellen Fehlermöglichkeiten identifiziert und analysiert werden. Diese Zusammenarbeit trägt auch dazu bei, dass Abhilfemaßnahmen effektiv umgesetzt werden.
- Dokumentation. Die Ergebnisse der FMEA sollten dokumentiert werden, einschließlich der identifizierten Fehlerarten, ihrer Ursachen und Auswirkungen sowie der empfohlenen Korrekturmaßnahmen. Diese Dokumentation trägt dazu bei, dass das durch den FMEA-Prozess gewonnene Wissen erhalten bleibt und für zukünftige Verbesserungen genutzt werden kann.
Durch die Einhaltung dieser Schlüsselprinzipien unterstützt die FMEA Unternehmen dabei, mögliche Fehler zu identifizieren und zu minimieren, die Produktqualität und -zuverlässigkeit zu verbessern und die Kosten im Zusammenhang mit Produktrückrufen, Garantieansprüchen und Kundenbeschwerden zu senken.
FMEA-Vorteile und -Nachteile
Hier sind einige seiner Vor- und Nachteile:
Vorteile:
- Frühzeitige Erkennung von potenziellen Fehlern. Bevor sich tatsächliche Probleme entwickeln, kann die FMEA dabei helfen, mögliche Probleme während der gesamten Konstruktions- oder Produktionsphase zu erkennen. Die frühzeitige Erkennung möglicher Probleme macht deren Behebung einfacher und weniger kostspielig.
- Verbesserte Produkt-/Prozessgestaltung. Die FMEA kann dazu beitragen, die Gesamtqualität des Endprodukts zu erhöhen, indem mögliche Probleme frühzeitig im Entwurfs- oder Produktionsprozess erkannt werden.
- Verbesserte Kommunikation. Durch die FMEA müssen verschiedene Interessengruppen in den Risikomanagementprozess einbezogen werden, was ihre Interaktion und Zusammenarbeit verbessern kann.
- Kostengünstig. Kosten im Zusammenhang mit der Entdeckung und Behebung von Fehlern, Garantieansprüchen und Rückrufaktionen können mit Hilfe der FMEA gesenkt werden.
Benachteiligungen:
- Zeitaufwendig. Die FMEA ist ein umfassendes und zeitaufwändiges Verfahren, dessen Durchführung viel Arbeit und Ressourcen erfordert.
- Begrenzter Umfang. Die Wirksamkeit einer FMEA hängt von den Informationen ab, die zum Zeitpunkt ihrer Durchführung verfügbar sind. Sie kann nicht für unvorhergesehene oder unvorhersehbare Bedrohungen geplant werden.
- Übermäßiger Rückgriff auf subjektive Beurteilungen. Da die FMEA die Verwendung von Expertenmeinungen und Annahmen erfordert, kann die Risikobewertung voreingenommen und anfällig für Subjektivität werden.
- Fehlender Kontext. Die FMEA erfasst möglicherweise nicht alle möglichen Fehlermodi, insbesondere wenn das Verfahren übereilt ist oder die Analysten nicht über die nötige Ausbildung oder Fachkenntnisse verfügen.
FMEA-Änderungen und -Erweiterungen
Dieser Prozess wird in der Praxis oft nicht in seiner Rohform angewendet. Im Laufe der Jahre hat der FMEA-Prozess verschiedene Änderungen und Erweiterungen erfahren. Einige gängige Beispiele sind:
- FMECA (Failure Mode, Effects, and Criticality Analysis) ist eine Erweiterung der FMEA, die eine Stufe zur Bestimmung der Kritikalität oder des Schweregrads jedes Fehlermodus auf der Grundlage einer Kombination aus Auftreten, Entdeckbarkeit und Folgen hinzufügt. Die Priorisierung der wichtigsten Fehlermodi, die dringend behoben werden müssen, wird durch die Kritikalitätsanalyse erleichtert. In Branchen und sicherheitskritischen Systemen, in denen ein Ausfall schwerwiegende Folgen hat, wird FMECA häufig eingesetzt.
- IME(C)A (Intrusion Modes and Effects (and Criticality) Analysis) ist ein Risikobewertungsansatz, der zur Analyse der Sicherheit und Widerstandsfähigkeit von physischen Schutzsystemen (PPS) gegen Eindringversuche von Angreifern verwendet wird. IMECA wird häufig in Hochsicherheitsgebäuden eingesetzt, in denen Sicherheitsverletzungen schwerwiegende Auswirkungen haben können, wie z. B. in Kernkraftwerken, militärischen Einrichtungen und Regierungsgebäuden.
- Die Prozess-FMEA ist eine FMEA-Variante, die sich auf die Untersuchung wahrscheinlicher Fehlermodi in einem Herstellungs- oder Produktionsprozess im Gegensatz zu einem System oder einem Produkt konzentriert. Die Prozess-FMEA hilft bei der Identifizierung prozessbezogener Risiken, die sich auf die Qualität, Effektivität oder Produktivität des Prozesses auswirken können, sowie bei der Entwicklung von Korrekturmaßnahmen zur Abwendung oder Verringerung solcher Risiken.
- Die Konstruktions-FMEA untersucht wahrscheinliche Fehlerarten in der Konstruktionsphase eines Systems oder Produkts und nicht während des Herstellungs- oder Produktionsprozesses. Die Konstruktions-FMEA hilft bei der Identifizierung konstruktionsbezogener Risiken, die sich auf die Funktionalität, Sicherheit oder Zuverlässigkeit des Systems oder Produkts auswirken können, und bei der Entwicklung von Konstruktionsänderungen oder -verbesserungen zur Beseitigung oder Reduzierung solcher Risiken.
- Die Software-FMEA ist auf Softwareentwicklungsinitiativen anwendbar und hilft bei der Identifizierung möglicher Fehlermodi während der Phasen des Softwaredesigns, der Kodierung, des Testens und des Einsatzes sowie bei der Entwicklung von Abschwächungstaktiken zur Beseitigung oder Minimierung solcher Risiken. Wenn Software für die Leistung und Sicherheit eines Produkts von wesentlicher Bedeutung ist, wie z. B. in der Automobilindustrie, der Luft- und Raumfahrt und bei medizinischen Geräten, wird die Software-FMEA häufig eingesetzt.
Warum die FMEA auch heute noch relevant ist
Obwohl es die FMEA schon seit über 70 Jahren gibt, ist sie immer noch ein relevantes und wertvolles Instrument für viele Branchen. Da Produkte und Prozesse immer komplexer werden, wird die Notwendigkeit eines proaktiven Risikomanagements immer wichtiger. Die FMEA ist aus mehreren Gründen auch heute noch relevant:
- Risikomanagement. Die FMEA hilft Organisationen dabei, potenzielle Risiken im Zusammenhang mit einem Produkt, einem Prozess oder einem System zu identifizieren und zu mindern. Sie hilft bei der Identifizierung von Fehlermöglichkeiten und deren Auswirkungen auf das System sowie bei der Bestimmung der Wahrscheinlichkeit ihres Auftretens.
- Qualitätsverbesserung. Die FMEA kann zur Verbesserung der Qualität von Produkten, Prozessen und Systemen eingesetzt werden, indem potenzielle Probleme identifiziert und proaktive Schritte unternommen werden, um ihr Auftreten zu verhindern. Dies kann dazu beitragen, Fehler zu reduzieren, die Kundenzufriedenheit zu erhöhen und die allgemeine Produktzuverlässigkeit zu verbessern.
- Einhaltung gesetzlicher Vorschriften. Viele Branchen, wie z. B. das Gesundheitswesen und die Automobilindustrie, verlangen FMEA als Teil ihrer gesetzlichen Vorschriften. Mit Hilfe der FMEA kann sichergestellt werden, dass Produkte und Prozesse die erforderlichen Sicherheits- und Qualitätsstandards erfüllen.
- Kosteneinsparungen. Durch die frühzeitige Erkennung potenzieller Probleme im Entwicklungsprozess kann die FMEA Unternehmen helfen, kostspielige Fehler und Nacharbeiten zu vermeiden. Dies kann auf lange Sicht zu erheblichen Kosteneinsparungen führen.
Schlussfolgerung
Zusammenfassend lässt sich sagen, dass die FMEA ein leistungsfähiges Instrument ist, das Organisationen dabei helfen kann, potenzielle Fehler zu vermeiden, bevor sie auftreten, und sicherzustellen, dass sie auf alles vorbereitet sind, was schief gehen könnte.
Categories
About the author
Share
Benötigen Sie einen Projektkostenvoranschlag?
Schreiben Sie uns, und wir bieten Ihnen eine qualifizierte Beratung.